Cross Jeans Chose Permak Drying System
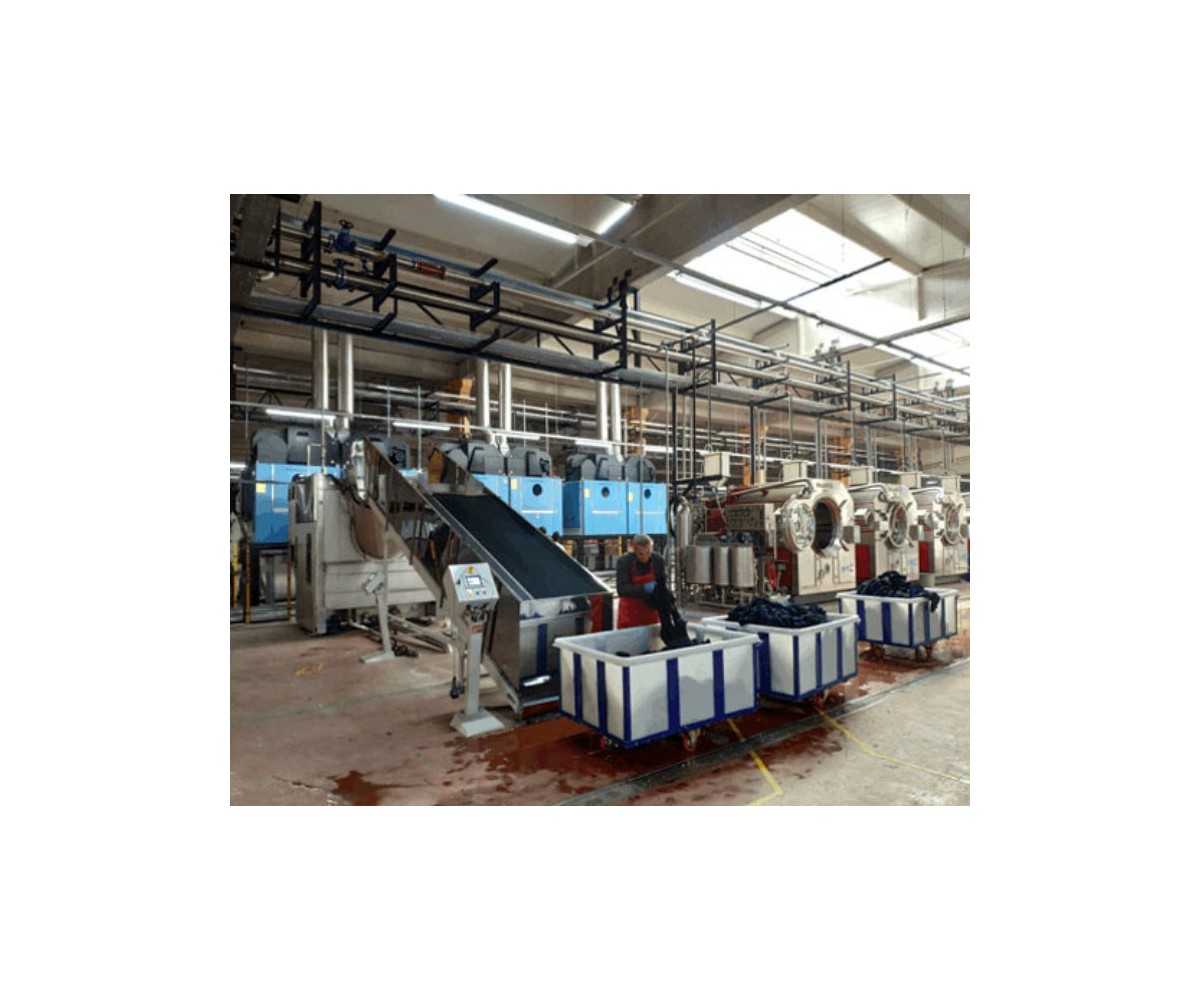
Permak Textile Washing, Spinning, and Drying Processes
- Minimum 15-20% Investment Savings (with fewer machines and less space required)
- Minimum 20-25% Labor Savings
- Minimum 30-35% Energy Savings
Permak A Plus Class Textile Cleaning and Finishing Systems offer significant savings:
Classic Jean Washing Facility Process Flow Details
In conventional jean washing systems, after stone, enzymatic, and chemical washing processes are completed in machines selected according to capacity and load distribution, textiles are transported by specially designed cranes to centrifugal spinning machines. There, they are manually placed in a balanced manner for spinning. Subsequently, the spun textiles are again removed by cranes and transferred to the drying line, manually loaded into dryers, and once dry, manually unloaded and sent to the inspection and finishing departments.
For all these operations, a medium-sized facility typically employs 5-6 people in the centrifugal spinning line and 3-4 people in the drying line. The drying process in the machines takes approximately 50-55 minutes, and with loading and unloading, the entire process is completed in about 1 hour.
During the spinning, drying, and inter-transportation steps, operations are susceptible to potential human errors and possible workplace accidents. Issues such as workplace accidents involving cranes and excessive textile drying and shrinkage due to incorrect manual program entry into machines can occur.
Modern Permak Jean Washing Facility Process Flow Details
In modern Permak textile systems, all stages, especially after the washing processes, are performed automatically. The system, equipped with an average of 1 centrifugal spinning machine with a 120 kg/load capacity and 6 drying machines of 120 kg each, along with conveyor equipment, provides a real output capacity of over 2,000 kg/hour.
The process steps are as follows:
- Washed textiles are loaded onto a specially selected automatic loading conveyor. This conveyor, which can be integrated with a barcode reader, determines which programs should be applied in subsequent steps based on the textile code, transmitting the necessary information to all machines in the line. This effectively prevents potential human errors. An additional weight measuring system on the loading conveyor allows for accurate load capacity selection or input control proportional to the load.
- After the loading conveyor, the textiles are spun in specially designed centrifugal machines without requiring any manual intervention. Achieving high spin speeds (G's: 800), the spinning process can be completed in 2.5 to 3.0 minutes with no labor required.
- Following the spinning process, a distribution elevator automatically transfers the textiles to a drying machine selected by the system, again with no manual intervention needed. The textiles are then dried with programs corresponding to the transferred textile information.
- The final units of the system, the drying machines, are specially designed and integrated with energy recovery systems. This allows them to complete the drying process in approximately 20 minutes, which translates to three times the capacity output compared to classic machines. These units also consume 30-50% less energy thanks to special exhaust recirculation systems.
- In medium-sized facilities, classic systems require 5-6 people in the centrifugal spinning line and 3-4 people in the drying line for all these operations. With Permak systems, the modernization investment, achieved through savings in personnel and energy, will amortize itself in a very short period.