Possible Problems in Industrial Drying Machines
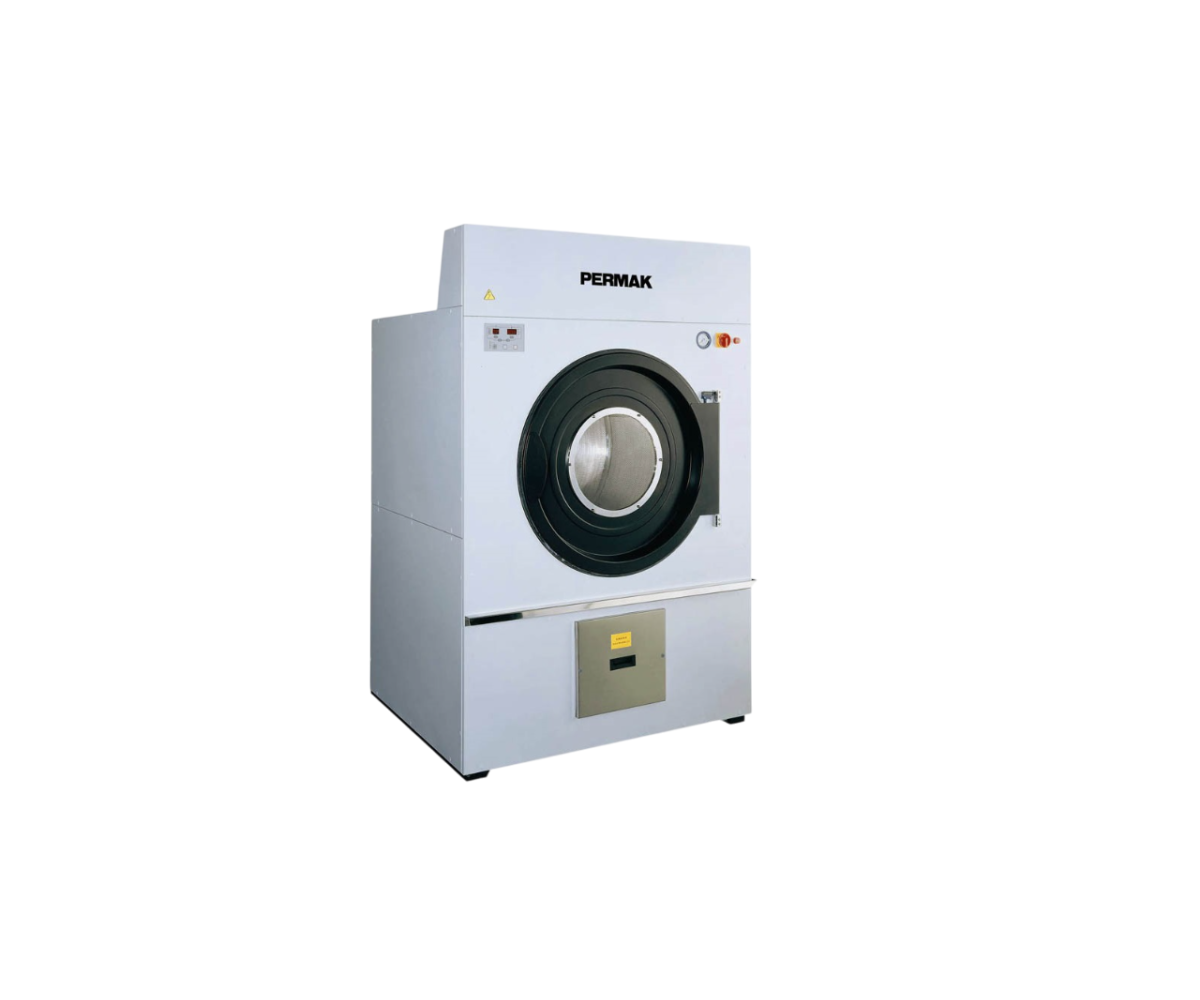
These machines, which are used in industrial laundries for drying laundry that does not need to be ironed or that needs to be pre-dried before ironing, are called "drum dryers". Their working principle is to dry the laundry with hot air circulation while the laundry is spinning in the drum. They have single-door, separate loading and unloading doors or tilting models in various capacities. They are heated by electricity, steam or gas. Their drums are generally made of stainless steel.
Apart from these, tunnel type dryers are also widely used. They can be used to dry clothes and remove wrinkles. Clothes enter from one side of the tunnel and exit from the other. The movement of the clothes is done by moving them on the pipe of the hangers on which they are hung. Their working principle is to dry the clothes with hot air circulation or only dry air currents at normal temperature. Problematic or very special care clothes are dried with the help of air currents at normal temperature.
The most commonly used heater to obtain hot air in drying machines is steam.
Steam-Related Issues and Solutions in Industrial Drying Machines in Laundries
- • Insufficient steam production capacity in the steam boiler or steam generator due to ageing or inefficiencies, increased steam load in the overall plant, or steam leaks.
- • Pressure fluctuations and steam pressure drops in machines due to the use of undersized pipelines.
- • Inappropriate design of branch pipes, especially after steam pressure reducing valves, leads to steam shortage and delayed heating.
- • Choosing small diameter condensate lines will cause inadequate condensate drainage, water accumulation and water hammer.
- • Lack of insulation in steam and condensate lines.
- • Live steam leaks from steam traps.
- • Insufficient pressure in the machines due to jamming during steam drawing of more than one machine from the same branch.
- • Unequal distribution of steam load in main line and branches - incorrect engineering.
- • Lack of sufficient margin for possible future capacity expansion.
- • Incorrect slope of steam mains, branches and other pipelines.
- • Condensate build-up and delayed heating/increased fuel bills due to incorrect type and/or undersized steam trap.
- • Inadequate discharge or inadequate steam inlet due to blockage of the strainers before the steam trap and pressure reducer.